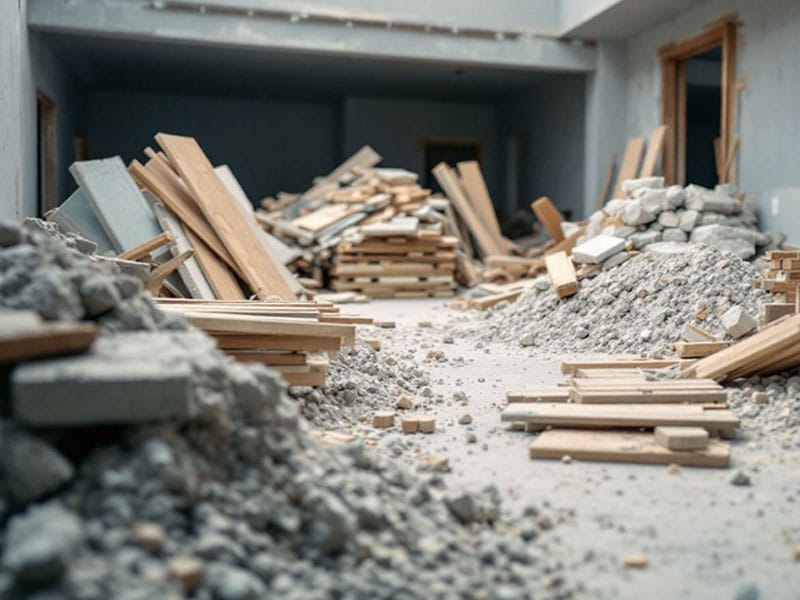
The Hidden Costs of Delaying Construction Debris Removal
Delaying the cleanup of construction debris can throw your entire project off track.
Piles of materials like concrete, wood, and drywall aren’t just unsightly—if ignored, they can lead to costly problems.
This guide discusses how postponing waste removal affects timelines, safety, and finances—and what you can do about it.
Key Takeaways
- Delaying debris removal increases costs, such as labor overtime, equipment rentals, and storage fees. OSHA violations can result in fines starting at $15,625 per violation.
- Accumulated waste blocks work areas, slows productivity by up to 30%, and causes delays in material deliveries or project timelines.
- Cluttered sites pose safety risks like trips or falls and increase insurance premiums due to workplace hazards.
- Poor disposal practices lead to environmental damage, regulatory fines, and legal liabilities for site owners or contractors.
- Proper debris management improves efficiency, meets compliance rules (OSHA/EPA), and maintains a professional image for clients.
Critical impact on project timelines
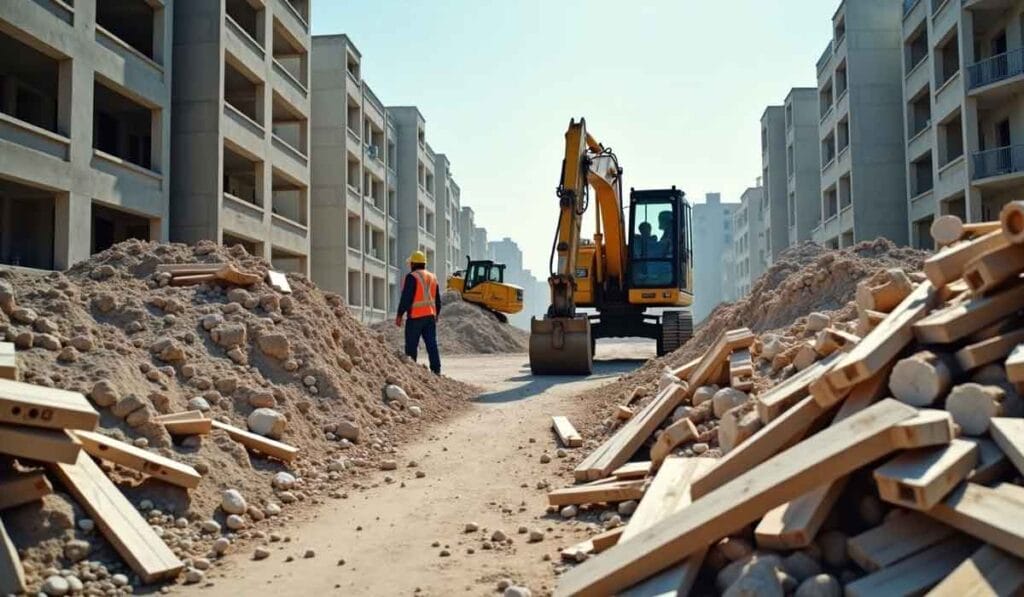
Piles of construction debris hinder your project. Workers waste time moving through cluttered sites, reducing productivity.
Labor costs increase as delays extend timelines.
Accumulated materials obstruct equipment and create logistical challenges.
Obstructed areas delay material deliveries or require rescheduling.
Construction dumpster shortages add storage difficulties, causing further delays.
“Effective waste removal is essential to keeping your schedule on track.”.
Overview of debris types (concrete, masonry, wood, metals, drywall)
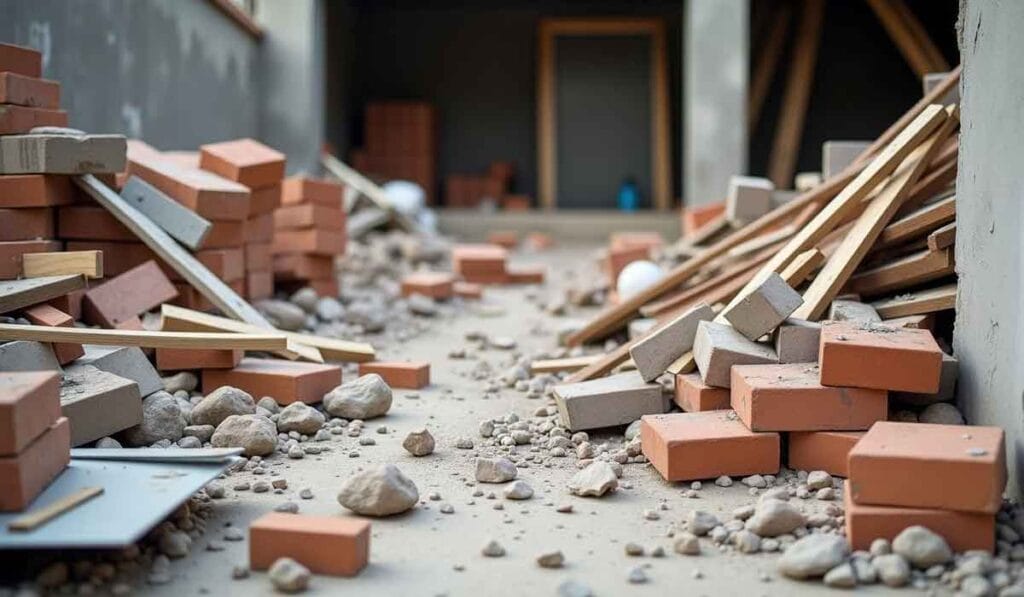
Construction sites produce different types of debris.
Each material needs proper handling to avoid safety hazards and project delays.
- Concrete pieces are heavy and take up space. Improper disposal can contaminate water or damage ecosystems.
- Masonry waste, like bricks and ceramics, can block paths and limit storage space if left unattended.
- Wood scraps can become safety hazards or fuel for accidental fires on-site if neglected.
- Metals, such as steel beams or pipes, increase the risk of injury due to sharp edges when scattered around.
- Drywall fragments release dust particles into the air, reducing air quality and causing health problems for workers.
Untouched debris can hurt your schedule and compliance efforts, impacting overall timelines.
Real costs beyond basic cleanup expenses
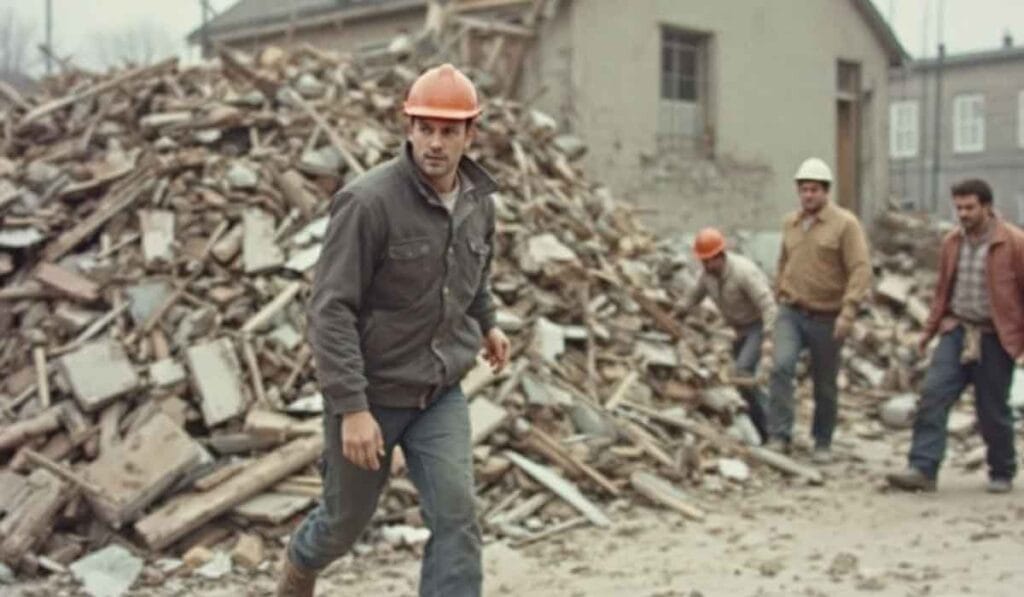
Large piles of construction waste cost more than basic cleanup bills.
Delayed debris removal often leads to higher labor costs, as workers may spend extra hours sorting, moving, or working around the mess.
Improper waste disposal can also produce fines from agencies like OSHA or the EPA.
Hazardous materials left unattended increase the risks of spills, further raising environmental remediation expenses.
Junk removal delays affect equipment rentals as well. Unused machinery sitting idle racks up charges daily.
Toxic pollutants from chemical leaching can contaminate nearby water and soil, adding liabilities for site owners and contractors.
Insurance premiums may rise due to increased workplace hazards or legal claims tied to negligence in managing recyclable materials safely.
Project Timeline Impacts
Delaying debris removal slows down your project’s progress.
Piled-up waste blocks work areas and affect your team’s efficiency.
Schedule disruptions from accumulated materials
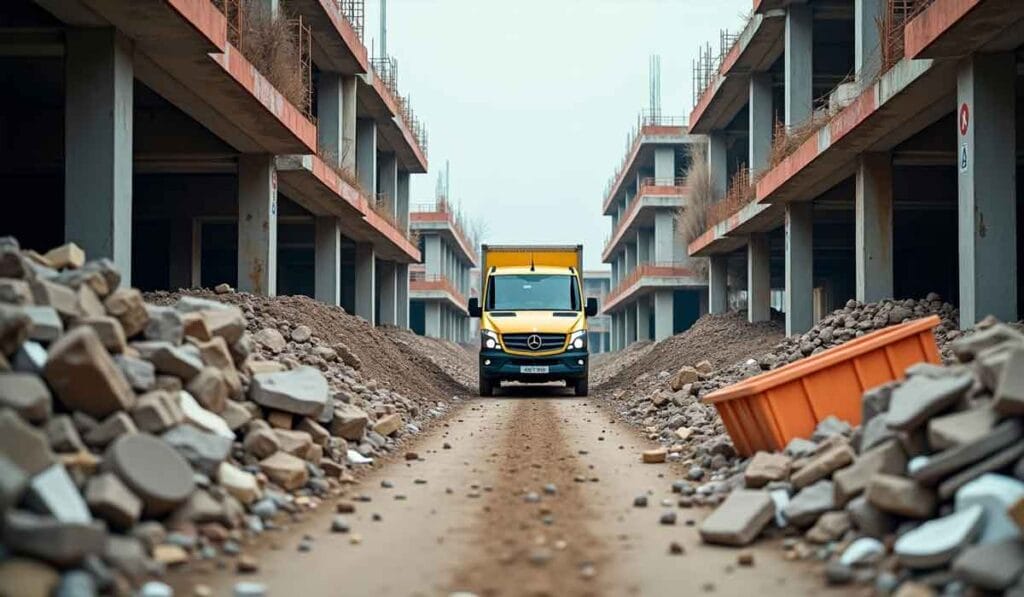
Piles of construction debris slow down your schedule.
Workers spend extra time maneuvering through cluttered sites, lowering efficiency.
Waste also blocks pathways, preventing the smooth movement of equipment and materials.
Delivery drivers may face delays as a result, further throwing off timelines.
Accumulated materials create storage issues.
Tools and supplies can be misplaced in the mess, wasting search time.
Clearing space for incoming materials becomes harder and disrupts planning.
These setbacks impact your project’s timeline, affecting labor productivity next.
Labor productivity effects
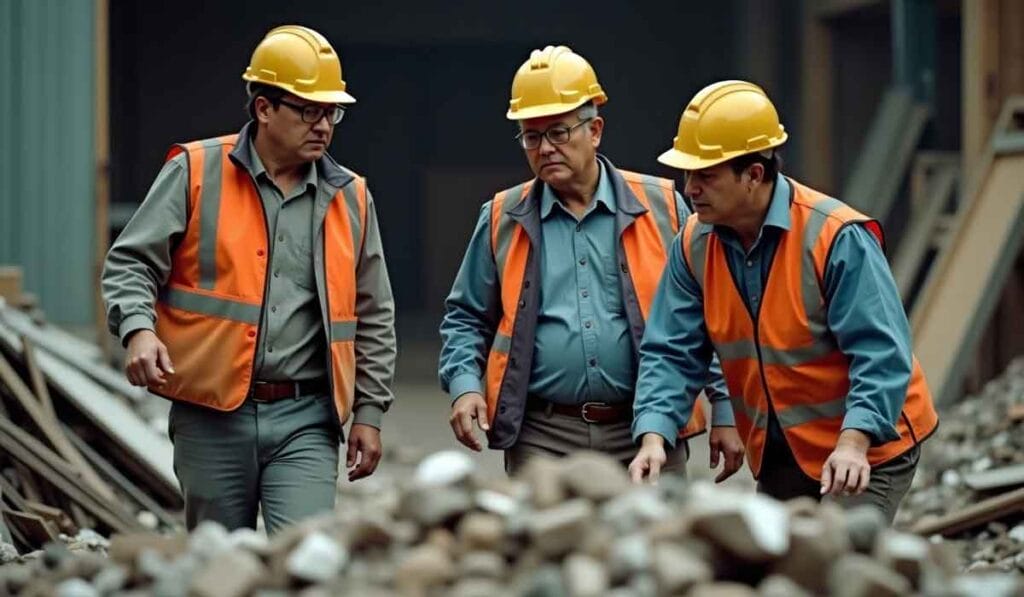
Accumulated construction debris slows down workers. Moving around waste adds time to tasks and increases fatigue.
Workers spend extra energy steering clear of hazardous materials, impacting efficiency.
Cluttered sites risk accidents, which reduce labor output.
OSHA compliance requires safe work areas, but debris buildup makes this harder.
Effective construction debris removal keeps your team productive and safe.
Material delivery complications
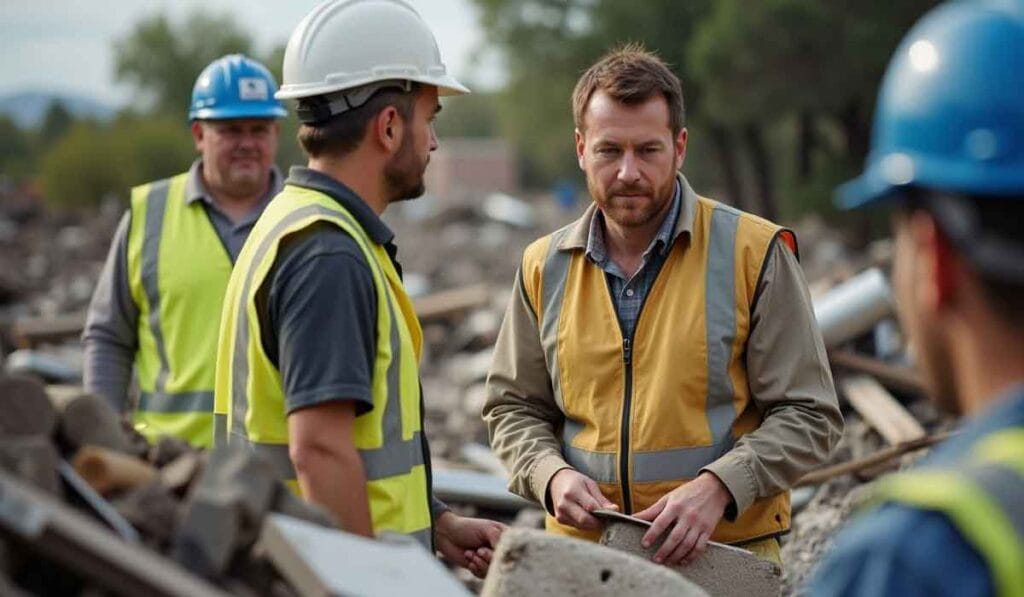
Debris piles can block access to delivering new materials.
Due to limited space, trucks may struggle to unload, causing delays and increased labor costs.
This interrupts your schedule and slows progress.
Workers waste time clearing the area instead of staying on task.
Suppliers might charge surcharges if they wait too long at cluttered sites or make multiple trips.
Tight areas also increase safety risks for delivery crews and workers nearby.
Poor waste management disrupts traffic flow, raises expenses, and affects project deadlines.
Storage space limitations

Accumulating construction debris eats up valuable storage space.
This limits room for new materials and hinders efficient site organization.
Crowded areas slow down movement, increasing risks to worker safety and cutting productivity.
It also forces you to find extra space, raising costs.
Improper waste disposal in tight spaces violates the Environmental Protection Agency (EPA) ‘s compliance requirements.
You may face fines for blocking access or failing to separate recyclables like metals or drywall.
Clear out debris promptly to keep projects running smoothly and avoid delays caused by delivery complications.
Safety and Compliance Considerations
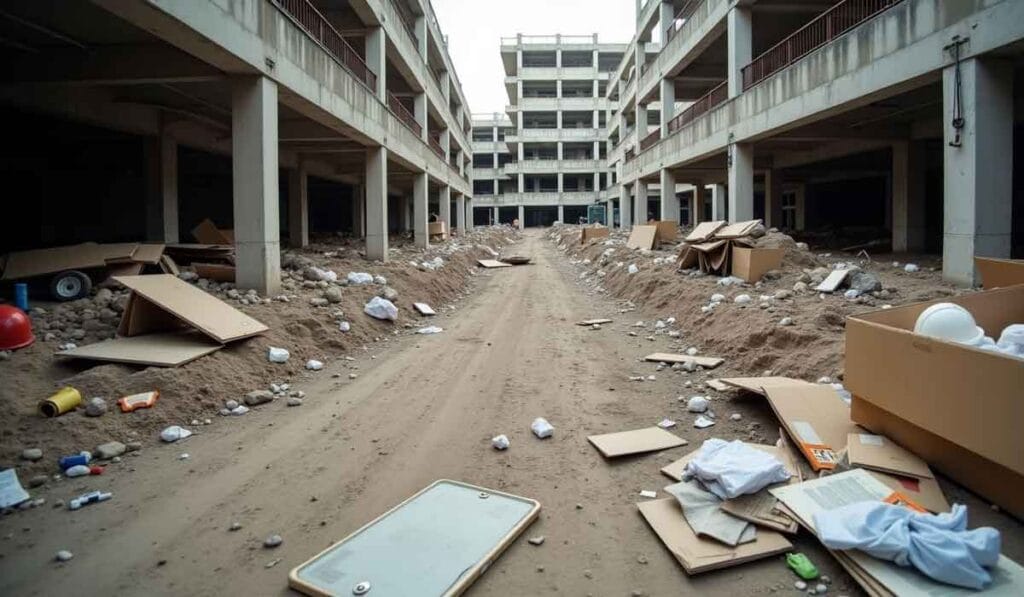
Ignoring debris removal can cause serious safety risks and costly compliance issues.
Workplace accident risks
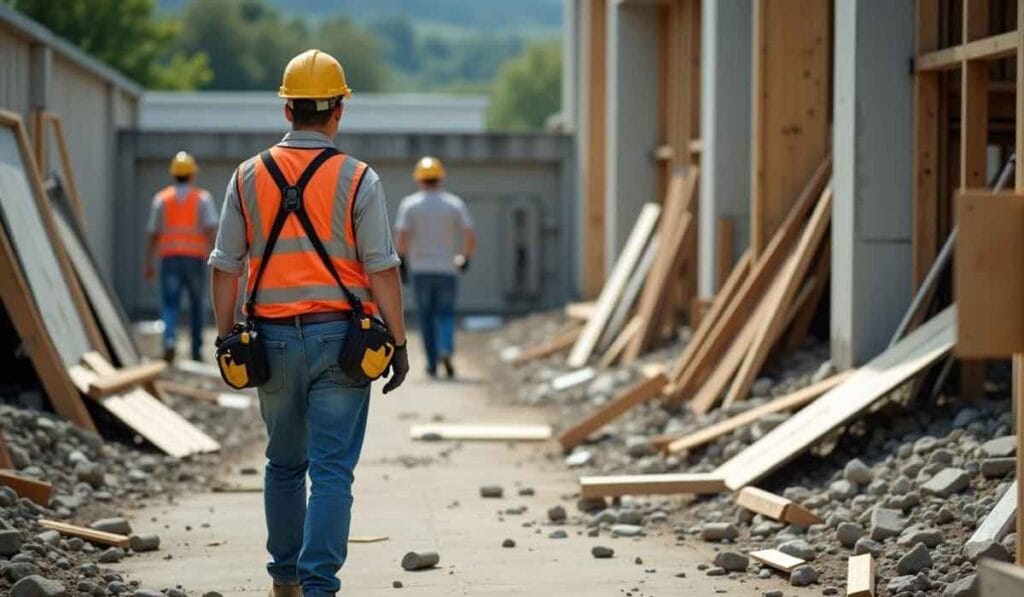
Accumulated construction debris creates serious safety hazards.
Workers can trip, slip, or fall over scattered materials like wood, drywall, or metals.
These accidents lead to injuries, medical expenses, and project delays.
OSHA requires safe working conditions and places strict rules on hazardous waste and material storage.
Improper waste disposal increases the risks of chemical exposure.
If improperly handled, hazardous materials, such as sharp metal pieces, can cause cuts or punctures.
Personal protective equipment (PPE) alone cannot fully protect workers from unorganized sites.
Clear debris quickly to reduce risks and ensure occupational safety for your employees.
OSHA compliance requirements
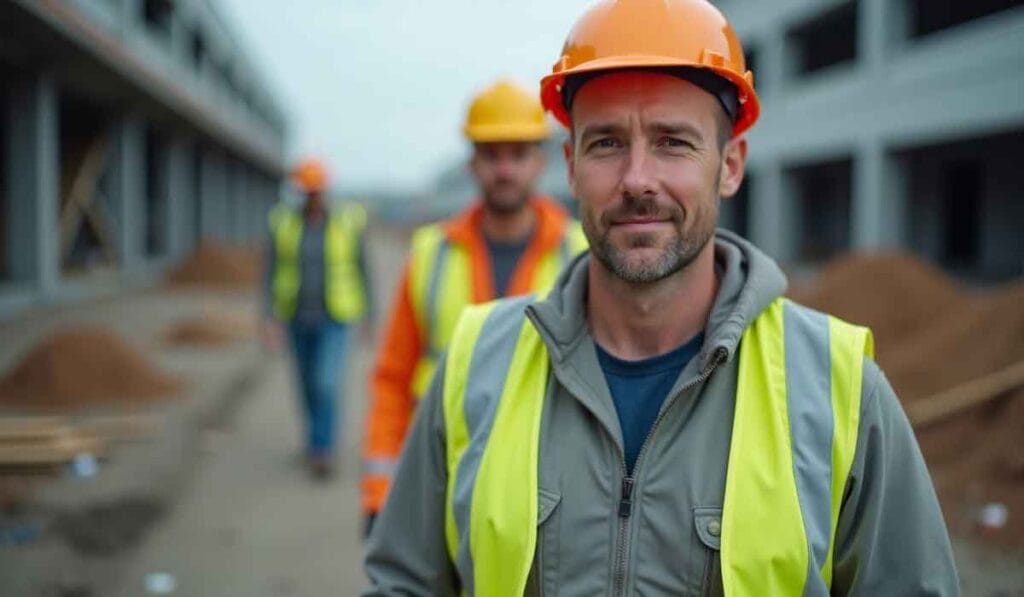
Failure to meet OSHA standards can result in hefty fines and penalties.
Construction debris left unchecked creates risks for workers, including trips, falls, or injuries from hazardous materials.
You must ensure your site follows proper waste handling rules to avoid accidents.
Use safety equipment and provide clear pathways around job sites.
OSHA also requires specific practices for handling hazardous waste, such as asbestos or chemicals.
Ignoring these rules increases legal liabilities and could harm worker health.
Proper construction debris removal protects your team while reducing compliance issues that could delay projects further.
Maricopa County regulations

Maricopa County enforces strict waste disposal regulations for construction sites.
Improper waste disposal can result in hefty fines or stop-work orders.
Construction debris like concrete, wood, and metals must go to approved recycling centers or landfills.
Illegal dumping is prohibited and affects water quality and soil health.
You must also follow hazardous waste management guidelines.
Materials that pollute the air or contaminate water need special handling.
These rules help reduce emissions and prevent damage to natural ecosystems.
Stay compliant to avoid financial risks while keeping projects on schedule.
Safety and compliance are key to maintaining smooth operations on-site.
Environmental code adherence
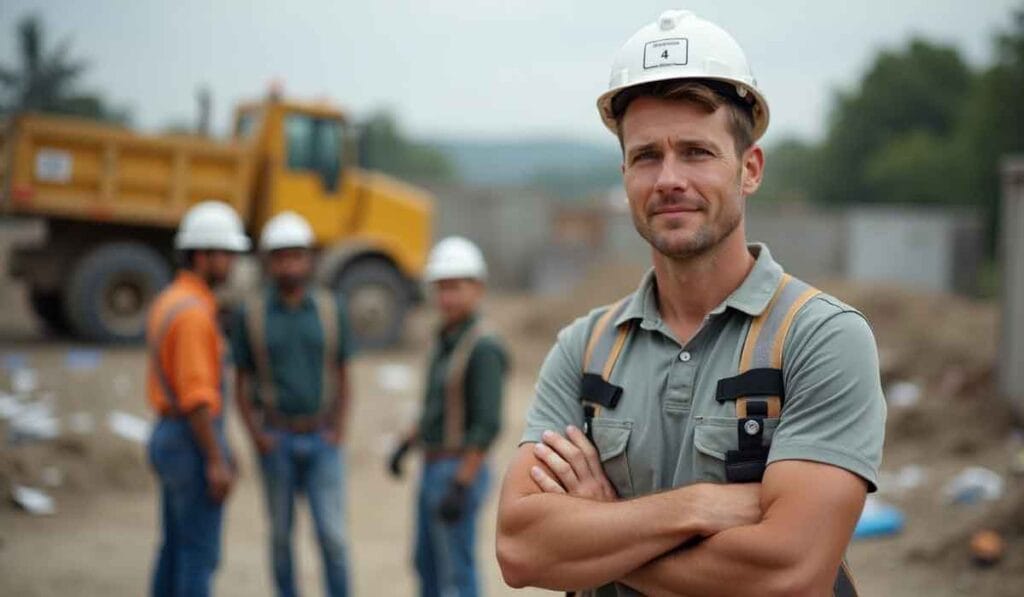
Following county regulations also means following environmental codes.
Improper waste disposal can contaminate water and harm local ecosystems.
Construction debris, like concrete or metal, may lead to soil degradation if left unchecked.
Compliance helps reduce air pollution from dust and harmful particles.
Avoiding fines for violations protects your budget.
Insurers may reject claims if you fail to meet these standards.
Use proper waste bins or trash bins to store materials safely on-site.
Insurance implications
Delaying construction debris removal can lead to increased insurance costs.
Accumulated debris raises workplace accident risks, which may result in higher premiums.
OSHA violations could also impact your coverage and make claims tougher to process.
Improper waste disposal can cause environmental damage, such as contaminating water sources.
This can lead to liability claims and legal fees.
Timely cleanup helps avoid these expenses while ensuring compliance with safety regulations.
Financial Impact Analysis
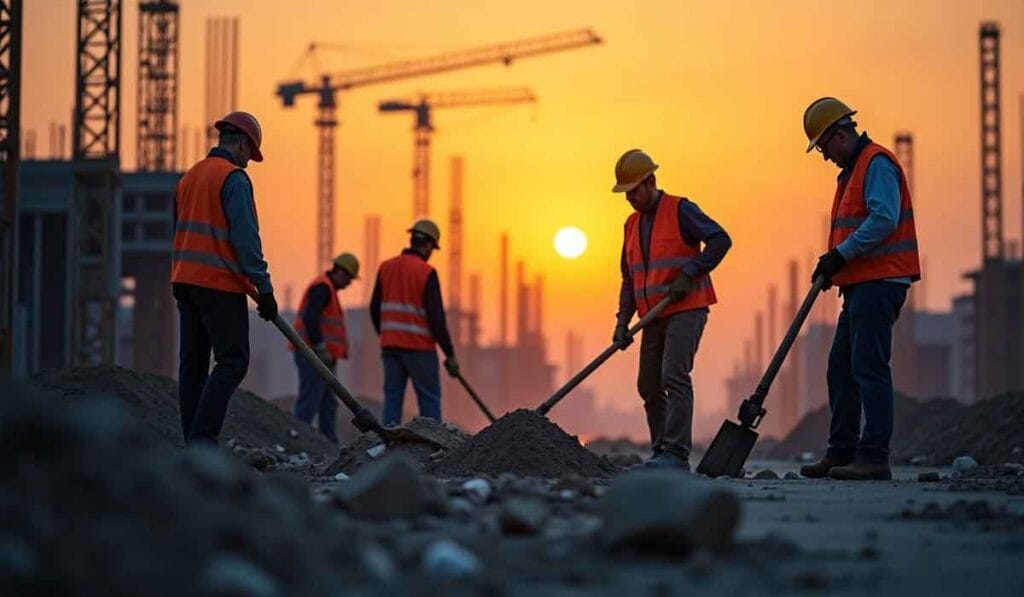
Delaying debris removal quickly increases costs.
You may pay for extra rentals, overtime, or storage fees.
Stay ahead to save money and avoid bigger problems.
Extended equipment rental costs
Holding onto rented equipment longer increases costs.
Machines like excavators or loaders come with daily fees that add up quickly.
Accumulated construction debris delays work and extends rental periods, denting your budget.
Overdue removal also keeps specialized tools tied up.
This can lead to project delays and higher labor expenses as workers wait for equipment access.
Managing debris efficiently reduces rental charges and prevents unnecessary expenditures on idle resources.
Labor overtime expenses
Labor overtime costs rise when construction debris piles up.
Workers spend more time dealing with clutter and slowing tasks.
Extended schedules mean paying higher wages outside regular hours.
These unplanned expenses can disrupt your project budget.
Preventing delays in construction debris removal reduces these risks.
Clear sites improve efficiency and keep labor costs manageable.
Address this to save money and maintain smooth operations, which will lead to understanding regulatory fines next.
Potential regulatory fines
Improper waste disposal can lead to significant regulatory fines.
OSHA enforces strict workplace safety rules, and failure to comply can result in penalties starting at $15,625 per violation.
Violating environmental codes by allowing construction debris to contaminate water or harm habitats may bring even higher fines.
Maricopa County and other local authorities often impose additional fees for non-compliance with their regulations.
These could include improper handling of hazardous materials or failing to remove debris on time.
Such expenses add up quickly and hurt your project’s budget.
Lost productivity calculations
Accumulating fines isn’t your only concern.
Delayed debris removal directly impacts productivity, reducing efficiency and increasing timelines.
Use the table below to understand how delays in removing construction debris can significantly hinder your team’s performance.
Higher labor hours cost up to 15% more | Effect on Productivity | Cost Implication |
---|---|---|
Cluttered Workspaces | Increases worker movement time | Higher labor hours costing up to 15% more |
Blocked Access to Equipment | Delays operational tasks | Idle machine costs: $100-$300 per hour |
Reduced Team Efficiency | Impacts job focus and morale | Productivity drops by 20%-30% |
Hazards from Debris | Interrupts ongoing tasks | Injury-related downtime costs $1,200/day |
Material Transport Delays | Slows down planned deliveries | Delivery rescheduling costs $500-$1,000 |
Storage space costs
Unused construction debris takes up valuable space.
Piles of concrete, wood, or drywall limit your storage areas.
This can delay material deliveries and disrupt workflows.
Renting extra storage units increases costs and eats into profits.
Delays increase labor expenses and slow contract progress.
Proper construction debris removal avoids these issues.
Focus on clear workspaces to reduce hidden costs like wasted time and effort.
Professional Site Management
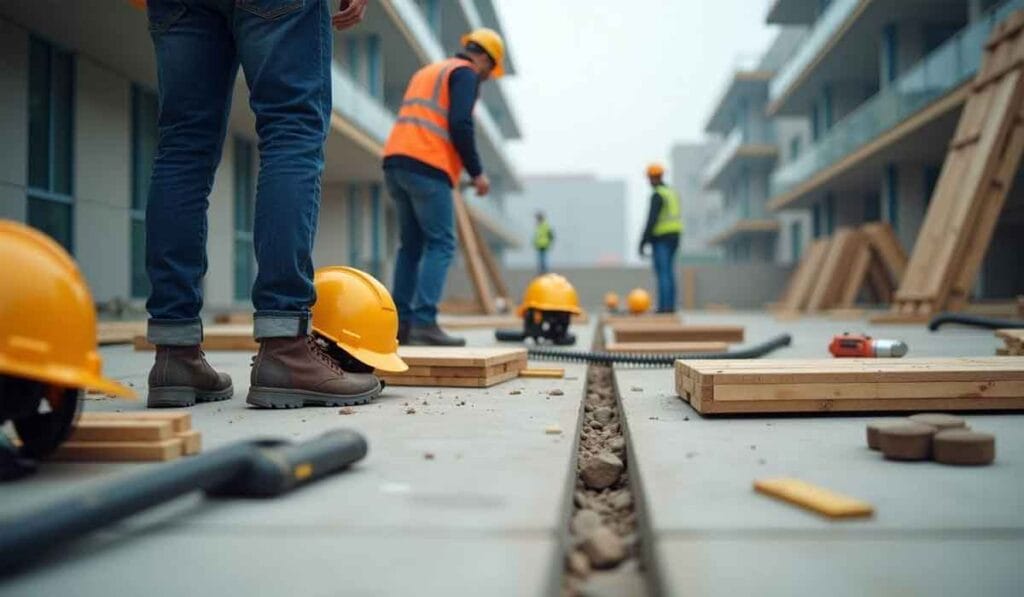
Proper site management keeps projects on track and reduces risks.
Explore ways to improve organization and maintain safety at your job site.
Site organization techniques
Organizing a construction site helps reduce project delays and keeps work smooth.
Well-managed sites save time and money and ensure safety.
- Clear debris daily to avoid waste accumulation that slows down progress. Regular rubbish removal improves site flow.
- Place containers close to work areas to minimize unnecessary trips. This saves labor time and increases productivity.
- Label bins for different materials, such as concrete, wood, and metals. Proper sorting supports reuse and reduces disposal costs.
- Ensure pathways are clear of obstacles to prevent worker injuries and meet OSHA safety standards.
- Organize storage zones for tools and materials based on priority use. Easy access lowers the risks of lost items or damaged goods.
- Create designated unloading areas for deliveries to speed up material handling. This reduces delivery disruptions and storage conflicts.
- Use signs to guide traffic flow on-site, avoiding vehicle accidents in busy environments.
- Limit hazardous materials exposure by isolating them from common paths or active zones.
- Keep heavy equipment parked away from foot traffic zones to maintain worker health and safety compliance.
- Plan your debris removal schedules with insured professionals to avoid fines for improper waste disposal or environmental code breaches.
Material sorting strategies
Sorting materials properly saves time and keeps your project moving.
It also helps reduce costs and ensures compliance with safety regulations.
- Separate hazardous materials like asbestos or lead-based paint. This avoids health risks and meets Occupational Safety and Health Administration (OSHA) rules.
- Keep recyclable items, such as metals or plastics, in a separate pile for efficient disposal or reuse. This lowers waste management expenses.
- Group similar debris types, such as wood, concrete, or drywall, to speed up removal logistics.
- Use clearly labeled bins or containers to organize debris on-site for quick identification.
- Avoid mixing contaminates that can harm water sources by isolating specific waste types.
- Place heavier materials like concrete at the bottom of storage areas to prevent damage to lighter debris above it.
- Sort reusable construction materials like bricks or lumber first to minimize material costs for future projects.
- Ensure all sorted piles are easily accessible so workers can move freely without disruptions.
- Regularly monitor storage density levels to avoid clutter affecting site traffic flow and labor productivity.
- Train your team on sorting practices to reduce errors that may lead to project delays or fines for improper waste disposal.
Container placement optimization
Properly placing containers on a construction site saves time and money.
It also improves safety and increases labor efficiency.
- Place containers near the work area to reduce workers’ mileage. This lowers labor costs by cutting down on walking time.
- Avoid blocking traffic flow by positioning containers away from main paths. This prevents accidents and delivery delays.
- Select flat, stable ground to avoid tipping or spills. This reduces the risks of workplace accidents and compliance issues with OSHA regulations.
- Use separate containers for hazardous materials like asbestos or chemicals. This simplifies sorting and prevents improper waste disposal fines.
- Keep container areas clean to avoid water contamination from runoff debris. Ignoring this can harm the environment and lead to fines in Maricopa County.
- Monitor container fill levels daily to prevent overflow into storage space. Overfilled bins can slow projects and increase medical expenses from safety hazards.
- Label all containers clearly to organize construction debris like wood, drywall, or metals faster, saving valuable project time.
- Ensure safe access routes for trucks picking up or delivering bins to avoid project delays or damage to property value.
Traffic flow management
Efficient container placement helps keep the site organized, but traffic flow management ensures smooth operations and safety.
Poorly managed site traffic can cause delays, accidents, and higher costs.
- Limit vehicle congestion by creating clear entry and exit points. Mark these areas with signs for better visibility and navigation.
- Restrict access to heavy machinery zones to prevent accidents. This reduces medical expenses from workplace incidents.
- Keep pathways open for essential deliveries. Blocked roads delay material delivery and increase project delays.
- Assign specific parking spaces for workers and visitors. Unplanned parking wastes space and impacts storage availability.
- Use traffic controllers during peak hours on larger sites. Proper coordination minimizes risks of collisions or equipment damage.
- Prevent improper waste disposal in driving areas by designating drop-off zones for construction debris removal.
- Plan routes to separate pedestrian paths from vehicle zones. Safety improves when people avoid heavy machinery lanes.
- Avoid sharp turns or narrow roads for trucks carrying hazardous materials or bulky loads like drywall or concrete debris.
- Ensure compliance with OSHA rules for worksite traffic control setups, reducing the risk of regulatory fines or shutdowns.
- Outsourcing traffic management to experts saves time while boosting productivity across residential construction sites.
Effective site planning helps you manage risks, improve efficiency, and maintain client satisfaction throughout the project timeline.
Client Relations and Project Success
Strong debris management boosts customer trust.
It helps ensure your projects finish on time, keeping clients happy.
Professional image maintenance
Delaying construction debris removal hurts your professional image.
A cluttered site shows poor management and neglect.
Clients notice improper waste disposal, which raises doubts about quality and safety.
It also increases complaints from neighboring properties due to environmental impacts like contaminating water or harming local biodiversity.
A clean site builds trust with clients and regulators.
Following compliance rules, such as OSHA or county regulations, shows responsibility.
Efficient construction debris removal protects property values while ensuring project success.
Keeping storage spaces organized improves workflows and enhances traffic flow on-site, leaving a lasting positive impression on everyone involved.
Project completion timelines
Accumulated construction debris slows projects.
Piles of concrete, masonry, wood, drywall, and metals block work areas, and laborers waste time dealing with these obstacles instead of staying productive.
Delays in clearing garbage push back material deliveries and disrupt schedules.
When waste piles up, storage space becomes scarce.
Equipment placement becomes difficult, and workflow suffers.
Missed deadlines risk client dissatisfaction and higher labor costs from overtime or extended rentals.
Effective debris removal keeps projects on track and ensures smooth operations.
Client satisfaction metrics
To build client trust, you must prioritize satisfaction.
Effective debris management directly influences how clients view your professionalism.
The table below highlights key metrics you should track to measure client satisfaction.
Metric | Description | Impact on Client Perception |
---|---|---|
Completion Time Accuracy | It builds transparency and fosters trust. | Delays can lower credibility and trust. |
On-Site Cleanliness | Level of organization and debris removal during work. | Messy sites give an unprofessional impression. |
Safety Standards | Compliance with OSHA and local safety regulations. | Ensures clients feel their investments are secure. |
Communication Updates | Regular updates on project status and milestones. | Builds transparency and fosters trust. |
Post-Project Property Value | The impact of cleanliness on property resale value. | Clean sites preserve and enhance client assets. |
Strong client relations improve project outcomes and open doors for future opportunities. Now, focus on the return on investment of proactive debris management.
Property value protection
Ignoring construction debris can lower property value.
Piles of waste, like concrete or wood scraps, make the site look abandoned.
This unattractive appearance discourages potential buyers or renters.
Improper waste disposal can also damage nearby land and water sources.
Contaminated areas reduce appeal and create costly issues for future owners.
You protect investments by managing construction debris removal quickly and properly.
ROI of Proactive Debris Management
Quick debris removal lowers risks and saves money.
Clean sites boost productivity and help you finish projects faster.
Cost-benefit analysis
Managing construction debris proactively saves costs and reduces risks.
Here’s a clear cost-benefit comparison to help you understand its value:
Category | Costs of Delayed Debris Removal | Benefits of Proactive Management |
---|---|---|
Labor Costs | Increased overtime expenses for cleanup. | Efficient scheduling reduces worker downtime. |
Equipment Rentals | Extended rental periods for tools and machinery. | Shorter rental durations save money. |
Compliance | Possible fines for OSHA violations and local code breaches. | Meeting regulations ensures no penalties. |
Material Delivery | Delays due to blocked access for suppliers. | Clear sites improve delivery timing. |
Storage Costs | Higher fees for additional on-site storage. | Free space allows better inventory control. |
Workplace Safety | Increased risk of accidents and liability claims. | Clean sites significantly reduce hazards. |
Project Timeline | Extended schedules lead to unhappy clients. | Faster project completion enhances satisfaction. |
Reputation | Damaged trust with clients due to delays. | Well-organized sites improve your professional image. |
Productivity gains
Clearing construction debris boosts efficiency.
Clutter slows down workers and increases labor costs.
Clean sites allow crews to move faster and stay focused on tasks.
Quick debris removal also prevents delays in material deliveries.
Open spaces make unloading easier, avoiding project delays.
You save time, cut overtime expenses, and improve productivity with proactive waste management strategies.
Risk mitigation value
Proactive debris removal reduces accident risks.
Piles of construction debris create hazards for workers and equipment.
OSHA fines can add up if you don’t follow safety regulations.
Avoidable injuries increase medical expenses and delay progress.
Improper waste disposal may contaminate water or harm nearby habitats.
Regulatory fines for such issues impact project budgets.
Smart risk management means staying compliant and protecting your team, the environment, and your bottom line.
Environmental benefits
Minimizing construction debris helps protect habitats.
Improper waste disposal leads to habitat destruction and loss of biodiversity.
Removing materials like concrete and drywall on time prevents harm to nearby ecosystems.
Proper construction debris removal reduces pollution.
Hazardous materials, if left unchecked, can contaminate soil and water sources.
Following compliance rules ensures cleaner surroundings for lasting environmental benefits.
Long-term client relationships
Strong debris management shows professionalism.
Clients respect organized, clean job sites without construction debris piling up.
It leaves a positive impression and builds trust in your work.
Delayed debris removal can lead to project delays or safety concerns, harming client satisfaction.
Proper handling keeps projects on schedule and adheres to compliance issues.
This helps secure repeat business and solidifies long-term relationships in the construction sector.
FAQs
1. What are the risks of delaying construction debris removal?
Delaying construction debris removal can lead to higher labor costs, project delays, and compliance issues with waste disposal laws.
2. How does improper waste disposal affect a construction project?
Improper waste disposal can cause hazardous materials to harm workers and result in medical expenses or fines for non-compliance.
3. Can doing it yourself save money on debris removal?
While doing it yourself may seem cheaper, it often increases average labor costs and risks handling hazardous materials improperly.
4. How does delayed debris removal impact the environment?
It can contribute to biodiversity loss due to pollution from leftover construction debris and unsafe disposal practices.
5. Are flat rates better for managing construction debris removal costs?
Flat rates help control expenses by offering predictable pricing while reducing the correlation between delays and rising costs.